The Evolving Philippine Engineering Labour Market for Australian Businesses in 2025
- Pierre Paul Collins
- Apr 5
- 9 min read
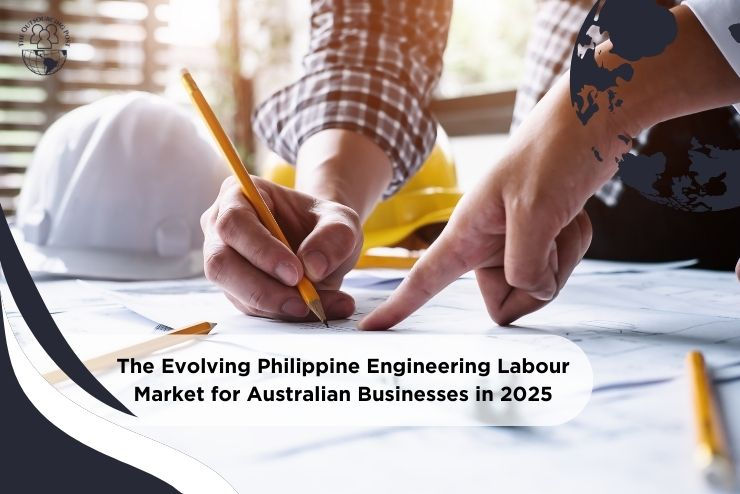
As of 2025, Australia’s engineering sector continues to grapple with severe skill shortages, rising labour costs, and project delays, putting pressure on infrastructure and commercial developments. Specialised fields—such as civil, mechanical, electrical, and software engineering—are among the hardest hit, forcing businesses to explore offshore solutions to stay competitive.
The Philippines has emerged as a key engineering talent hub, producing a steady pipeline of highly skilled professionals equipped to meet international demand. Universities now offer training in seismic design, tropical architecture, and disaster-resilient engineering, aligning with Australia’s growing focus on climate adaptation and resilient infrastructure. Meanwhile, an increasing number of Filipino engineers are trained in AS/NZS standards, ensuring technical alignment and seamless integration into Australian projects. The industry has also embraced technology-driven workflows, with more firms adopting BIM, Revit, Civil 3D, and automated compliance tools, making remote collaboration more efficient than ever.
Drawing from years of experience in global engineering talent strategies, this article explores the opportunities, risks, and best practices of offshoring engineering work to the Philippines. We’ll examine compliance with Philippine human resource management laws and regulations, quality assurance challenges, and how Australian businesses can strategically integrate offshore teams for optimal performance.
Why Australian Businesses Are Turning to the Philippine Engineering Workforce

As Australia’s engineering sector faces growing skill shortages and evolving demands for specialised expertise, businesses are increasingly turning to the Philippines. The Philippine engineering workforce is adapting to meet global needs, with a strong focus on areas like seismic design and disaster-resistant infrastructure, making Filipino engineers a crucial asset for Australian firms seeking to stay competitive in a rapidly changing market.
Addressing Australia’s Engineering Specialisation Gaps
Australia's engineering sector is struggling with critical skill shortages, with only 8.5% of engineering vacancies filled within a month in 2025 (Engineers Australia). This ongoing talent gap puts billions of dollars in infrastructure, energy, and advanced manufacturing projects at risk, leading to delays, budget overruns, and lost business opportunities.
The Philippines produces over 80,000 engineering graduates annually, many of whom are trained in specialisations directly relevant to Australian needs. Civil infrastructure engineers, for example, are in high demand for Australia's $110B transport infrastructure pipeline. What makes this even more valuable is the Philippine expertise in seismic design, tropical architecture, and disaster-resistant engineering, which aligns perfectly with Australia’s increasing focus on climate resilience.
For Australian firms, this presents an opportunity to fill talent gaps and enhance the quality of their engineering projects with professionals trained in critical specialisations. Businesses that leverage offshore engineering expertise can avoid project stalls, secure larger contracts, and improve their competitive edge in an industry where expertise is becoming harder to find.
Project Acceleration Beyond Cost Savings
While offshoring in the Philippines has long been associated with cost savings, in 2025, the real competitive edge lies in speed and efficiency. Australian engineering firms are now leveraging teams in the Philippines, not just to reduce expenses but to accelerate project delivery and scale smarter.
One of the biggest drivers is the 24-hour work cycle. Offshore engineers in the Philippines can pick up tasks at the end of the Australian workday and deliver progress by morning. This continuous handover process can reduce design and documentation timelines by 40–60%, eliminating downtime and keeping projects in motion around the clock.
In addition, collaboration technology has matured. Cloud-based platforms like BIM 360, Civil 3D, and Revit are now standard tools among offshore teams, minimising coordination errors and enabling real-time collaboration across borders. Many Filipino engineers also work in hybrid setups, combining the benefits of remote work with the structure of in-office environments—making communication with Australian teams more seamless and predictable.
With well-structured offshore teams, BIM coordination timelines have been cut from eight weeks to just three, allowing firms to take on more projects without compromising quality or deadlines. For Australian businesses, this speed means stronger client relationships, improved delivery performance, and increased profitability—without the need to expand the onshore workforce.
Technical Compatibility Advantages
A major concern for Australian firms considering offshoring is whether offshore engineers can work seamlessly within Australian standards and workflows. Fortunately, Philippine engineering education is closely aligned with AS/NZS standards, making the transition far smoother than with other offshore locations.
Filipino engineers also have strong expertise in Revit, Civil 3D, ETABS, and Tekla, often outperforming local talent in both availability and proficiency. This means Australian firms can
expand their talent pool without compromising on technical capability.
Another key advantage is English proficiency—ensuring that technical documentation is accurate, stakeholder communication is clear, and costly errors due to misinterpretation are
avoided. For businesses, this reduces the risk of expensive rework, legal compliance issues, and project delays, making offshore teams a strategic asset rather than just a cost-cutting measure.
Leveraging the Philippine engineering workforce allows Australian firms to tap into specialised expertise, accelerate project timelines, and integrate seamlessly with their technical and compliance requirements. This is more than just a solution to labour shortages—it’s a competitive advantage that enables engineering businesses to scale, innovate, and lead in an evolving market.
Challenges in Offshoring Philippine Engineering Talent

Offshoring engineering work to the Philippines offers a host of opportunities, but it also introduces specific challenges that can impact project quality and timelines. Having worked closely with both onshore and offshore teams, I've seen firsthand the complexities that arise when managing cross-border engineering projects. These challenges, while significant, can be mitigated with the right strategies and tools in place.
Engineering Quality Assurance Across Borders
One of the primary concerns in offshoring engineering tasks is ensuring that offshore teams consistently adhere to Australian Standards (AS/NZS). While Philippine engineers possess excellent technical skills, aligning with Australian regulatory requirements requires deliberate effort.
In past projects, I encountered challenges in transferring tacit knowledge—such as understanding local building conditions, climate considerations, and specific regional regulations—into the offshore team’s workflow. These nuances often weren’t readily available in documentation, creating gaps in compliance. For instance, in one major civil infrastructure project, we ran into delays because certain design elements failed to meet local environmental regulations, which required substantial revisions.
Maintaining professional certification compliance, such as with Engineers Australia, adds
another layer of complexity. Without a clear understanding of local accreditation requirements, it can become a bottleneck. Reports suggest that 40% of Australian businesses face difficulties when maintaining certification compliance with offshore teams, which is something I’ve observed personally. Establishing processes for managing these certifications from the start has proven essential to avoid legal and operational delays.
Additionally, understanding employment laws in the Philippines is critical. The regulations surrounding hiring, compensation, and benefits in the Philippines need to be navigated carefully to avoid any compliance issues. Offshoring providers familiar with these laws can help Australian businesses ensure smooth, legally compliant operations, safeguarding both their interests and those of their offshore teams.
Project Integration Complexities
Coordinating the seamless integration of onshore and offshore engineering teams is another area where challenges arise. A past project I managed highlighted the importance of version control and document management when working across time zones. With teams in Australia and the Philippines, the risk of losing track of revisions and updates was significant.
This challenge became evident during a large-scale infrastructure project where BIM coordination timelines were delayed by 3 weeks due to poorly managed version control. Adopting cloud-based collaboration tools allowed us to streamline the entire process, reducing document turnaround times by 40%, streamlining the entire process. Leveraging platforms like BIM 360 became indispensable in ensuring real-time feedback and version control, making it easier to integrate contributions from both teams effectively.
Cultural and Communication Nuances in Technical Contexts
Cultural differences can create subtle but impactful barriers in engineering collaboration. Filipino engineers often have a different approach to problem-solving and risk assessment, which can result in hesitancy when it comes to questioning design instructions or raising concerns. This cultural tendency to defer to authority can sometimes lead to critical issues being overlooked.
On one occasion, a major structural issue wasn’t flagged early on by the offshore team, which led to significant redesign work later in the project. To avoid these situations, I learned that fostering a culture of open communication is key. Ensuring that everyone feels comfortable voicing concerns, regardless of hierarchy, is essential to maintaining project integrity. Regular video conferences and collaborative problem-solving sessions became a crucial part of improving communication between teams and mitigating these challenges.
In addition, aligning technical terminology and documentation standards across different engineering traditions is essential for clarity. There have been times when differences in how terms are interpreted have led to confusion, which could have been avoided with more thorough alignment from the outset. Creating standardised design templates and terminology glossaries can significantly reduce these kinds of misunderstandings.
In overcoming these challenges, it’s clear that a proactive approach is required. Effective communication tools, cloud-based collaboration platforms, and a culture that values feedback are critical to ensuring smooth integration between onshore and offshore teams. With the right strategies in place, Australian businesses can harness the expertise of the Philippine engineering workforce while minimising risks and driving more efficient project outcomes.
Best Practices for Success in Offshoring Philippine Engineering Teams
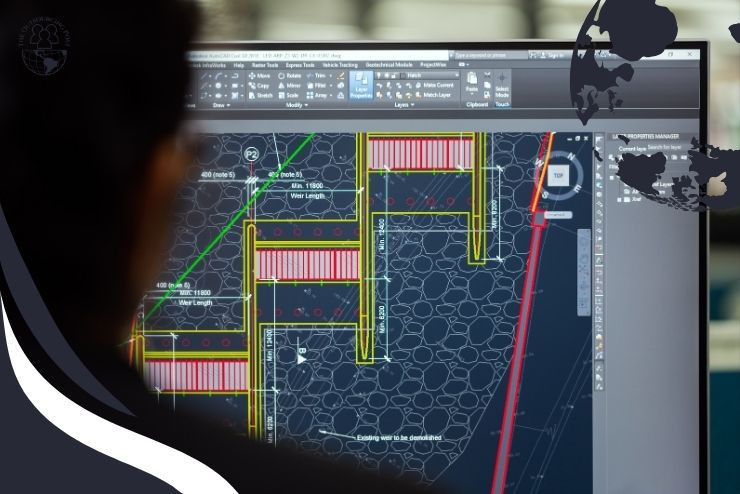
Successfully offshoring engineering tasks to the Philippines is not just about hiring skilled talent; it's about creating a seamless integration between Australian and Philippine teams. Through years of managing offshored engineering projects, I’ve discovered that putting structured systems in place and fostering strong collaboration is critical to success. Here are the best practices that Australian businesses can adopt to ensure their offshore engineering teams deliver consistently high-quality results.
Structured Engineering Capability Transfer Programs
The first step in setting up a successful offshore engineering team is ensuring that Filipino engineers are well-versed in Australian standards and methodologies. From my experience, standards immersion training is key—especially when it comes to Australian standards (AS/NZS codes). I’ve seen firsthand how a well-executed training program not only boosts the confidence of offshore engineers but also helps them apply local codes more accurately in their work.
In one project, we initiated a comprehensive training program focused on structural and civil engineering standards. This ensured that our offshore team was able to integrate seamlessly with the onshore team, reducing the revision cycle time by 30%. Additionally, creating standardised design review checklists tailored for cross-border collaboration is a simple yet effective tool. These checklists helped streamline the review process and ensured compliance across all design stages.
Another aspect that cannot be overlooked is shared knowledge bases. Australian businesses can benefit from developing knowledge repositories of local construction methodologies, climate considerations, and regional requirements. These resources not only speed up the onboarding process but also create a foundation for consistent and high-quality engineering output. In one instance, I introduced a shared database that included templates, engineering guidelines, and case studies. This became a go-to resource, ensuring that the offshore team could easily align their work with the local market’s needs.
Hybrid Team Structures for Optimal Integration
One of the most effective ways to ensure smooth collaboration between onshore and
offshore teams is by implementing hybrid team structures. Over the years, I've found that "pod" structures—where Australian lead engineers oversee technical teams in the Philippines—are the most efficient. This structure allows Australian engineers to provide direct guidance while leveraging the specialised skills of the offshore team.
In practice, this means that Australian engineers can focus on critical design decisions—those that directly impact the project’s quality, timeline, and regulatory compliance—while the offshore team handles more routine tasks like documentation, modeling, and analysis. For example, in a large-scale commercial project I managed, we assigned offshore teams to create detailed 3D models while the Australian engineers made final design decisions. This split allowed for faster project completion while maintaining high-quality standards.
Another important part of the hybrid structure is establishing liaison roles. These positions bridge communication gaps between Australian project managers and Philippine engineering teams. In a past project, this was crucial. Having a dedicated liaison helped ensure that project timelines, scope changes, and key decisions were communicated clearly across both teams, reducing confusion and enhancing workflow efficiency.
Technology-Enabled Quality Assurance Systems
With the right technologies in place, maintaining the quality of offshore engineering work becomes much easier. One of the best tools I’ve used is automated compliance-checking software. This technology ensures that designs comply with Australian codes and standards, providing an extra layer of confidence. I’ve worked with various automated systems that track compliance with AS/NZS codes, significantly reducing the risk of human error and ensuring that designs are ready for review much quickly.
Furthermore, cloud-based design review platforms like BIM 360 are essential for real-time collaboration and feedback. These platforms allow engineers to make annotations directly on models or designs, providing clear guidance for the offshore team and eliminating misunderstandings. In a recent infrastructure project, using BIM 360 allowed us to cut review times by over 50%, helping the project stay on schedule and on budget.
Finally, the advent of digital twin technologies has revolutionised remote site inspections and quality verification. I’ve seen how these technologies allow project managers to inspect and verify designs virtually, which can be especially useful for ensuring that offshore work meets Australian quality standards without the need for constant physical site visits. This level of remote verification ensures that potential issues are flagged early and addressed before they become critical.
Conclusion
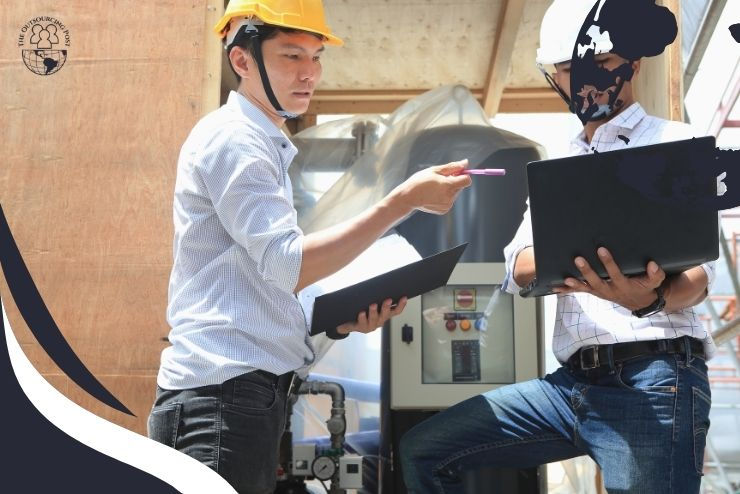
The Philippine engineering labour market has evolved into a highly specialised and globally competitive workforce, offering Australian businesses not only cost-effective talent but also advanced technical expertise. The rise of AS/NZS-certified Filipino engineers ensures quicker onboarding and seamless compliance while growing specialisations in disaster-resilient infrastructure, BIM, and sustainability that align with Australia’s shifting needs. The increasing adoption of technology-driven collaboration has made remote teamwork more efficient, accelerating project timelines and enhancing overall productivity.
A key hub in this transformation is offshoring in Clark, Philippines, where highly skilled engineering talent is readily available, and businesses can tap into a workforce that aligns well with Australian standards. For Australian engineering firms facing skill shortages and rising labour costs, tapping into the evolving Philippine talent pool presents a significant opportunity. Embracing this shift will provide speed, cost savings, and access to cutting-edge expertise. To stay competitive, Australian businesses must adopt the right integration strategies, ensuring compliance and seamless collaboration with offshore teams. With careful planning, the future of engineering project delivery can be both efficient and scalable.
Comments